8 Tips for Crusher Safety
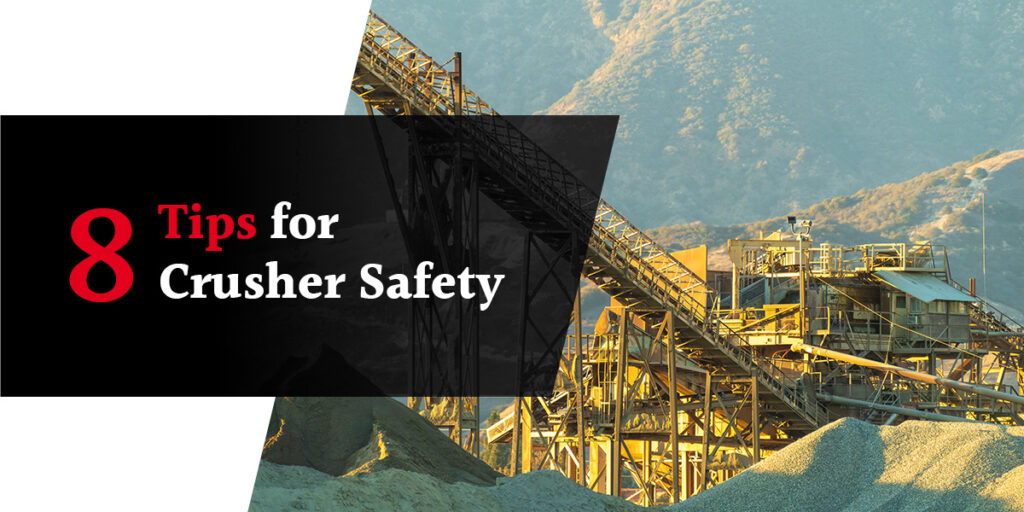
Crushing machines help reduce the size of rocks, concrete or construction rubble to safely dispose of debris or create material for production purposes. Every operator or employee who works with or around the equipment must receive full training in the stone crusher safety protocols of each machine. This will prevent hazardous messes or risky maneuvers from operators, including greasy platforms that could cause accidents or dirty equipment that might malfunction or break.
Here are eight crusher equipment safety tips for working with, cleaning up after and ending the operation of crushers.
1. Make Sure the Operator Is Fully Trained
When an operator does not receive adequate training, oversized material could enter the crusher and cause damage or the crusher could malfunction due to faulty management. Every operator must be thoroughly trained on feeding the machine and the specific type of crusher they are working with. This makes for a safer and more productive workplace. Ensure that operators keep detailed maintenance records that keep track of any issues with machinery.
2. Perform Regular Maintenance
Operate every crusher at an appropriate capacity to ensure rock crushing plant safety. Keep platforms and areas around the machine clean, and monitor the crusher’s lubrication, flow, temperature, wear and pressure at all times. If any hazardous debris exists after shutdown, clean the area to ensure safety and ease of maintenance. Check the workstation from all areas to ensure you’ve caught anything that appears risky or unsafe. Create a crusher safety checklist that every operator can use to adhere to company safety protocols in the workplace.
3. Feed Crushers Efficiently
All operators or employees working near the equipment should wear personal protective clothing, such as eye shields or safety belts. Eye shields can protect from flying debris or stones, and safety belts ensure that workers don’t fall into or near dangerous machines. Crushers should have all of their guards and safeties in place before operating. When feeding the machine, use choke, non-choke or trickle feeding when necessary and ensure you use the correct feed in primary, secondary and tertiary crushing methods.
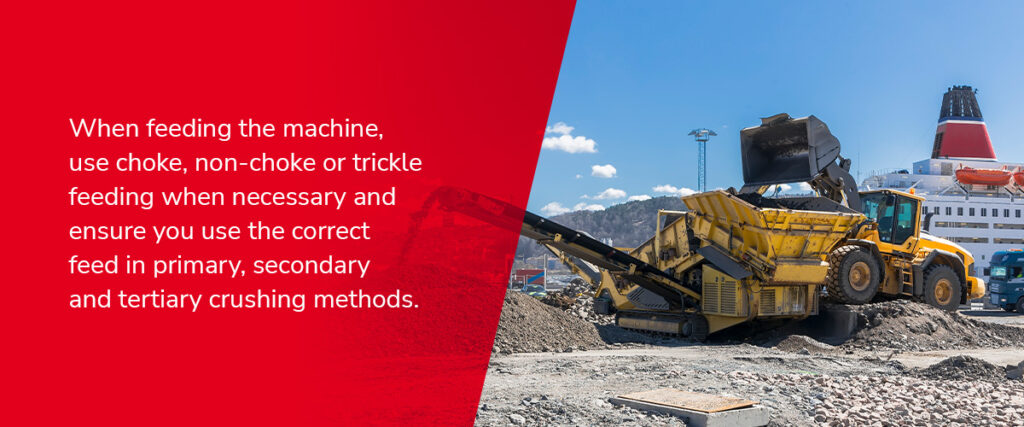
4. Keep the Operator Isolated
To ensure industrial rock crusher safety, operators can use an enclosed booth or a remote control station to remain isolated from dirt and debris that could harm the body or lungs. An enclosed cab should:
- Be well-sealed.
- Have proper ventilation.
- Use door jambs, proper joints and window grooves.
- Use an air filter.
- Include heating and air conditioning.
- Be kept clean to prevent settled dust.
5. Use Wet Spray Methods
Wet spray methods reduce the amount of silica exposure by positioning nozzles to thoroughly wet materials, making them easier to crush. For the best results, the size of the droplets should be large enough to wet the material thoroughly. Any nozzles used can include adequate water coverage without wasting water.
6. Perform Proper Shutdown Process
Ending the operation of a crusher is an essential part of crusher safety. There are a few steps to follow when shutting down a crusher that every trained worker should follow:
- Shut down the apron feeder.
- Ensure equipment is free of material.
- Shut down the primary crusher.
- Shut down the secondary crusher.
- De-energize the electromagnet.
- Shut off the dust collector.
- Close the valve to the water line.
After shutting down the crusher correctly, clean the machinery. Any greasy parts or dirty areas could cause workers to slip or hurt themselves. Make cleanups at the end of the day a consistent practice to lower employee hazards and risks.
7. Know the Three Stages of Reduction
It may be necessary for every operator to become familiar with the different kinds of crushers to ensure proper training and running of equipment while on the job. Crushers are typically divided into three categories that describe the phase of the crushing process and the crushing machine’s ability:
- Primary crushers: Primary crushers are the first stage in the crushing circuit. After the material is extracted from a mine, the primary crusher ensures the rock is broken down into a size the secondary crusher can handle. Types of primary crushers include jaw, cone, gyratory and impact crushers.
- Secondary crushers: Secondary crushers reduce the size of the material before the tertiary stage. Different feeding techniques might be necessary depending on how fine you want the material. Cone crushers are often used in this stage with consistent choke feeding methods.
- Tertiary crushers: This is the final stage of reduction in the crushing process. Tertiary crushing makes the material into a product. Types of tertiary crushers may include cone crushers, horizontal impact crushers or rolling crushers.
8. Learn the Common Types of Crushers
While various types of crushers exist, the four common types of crushers are the jaw, gyratory, cone and impact crusher. Each type plays a different role in the reduction process, and operators who work with crushing equipment should familiarize themselves with the structure and purpose of each type. Learn the various parts of jaw crusher safety, including how to successfully integrate concrete crusher safety protocols to better inform your work habits:
- Jaw crushers: Jaw crushers are blunt and often used in the primary crushing stage. They can break up large and hard materials but usually need a secondary crusher to make the rock finer.
- Gyratory crushers: Gyratory crushers have a conical head and a concave surface. They break through the material using compression methods and are often used at primary or secondary stations.
- Cone crushers: Cone crushers also work with the compression method, similar to the gyratory crusher. This kind of crusher contains a rotating mantle and a concave surface. It can accept dry or wet feeds depending on the material.
- Impact crushers: Impact crushers are used with less abrasive rocks. They use impact forces using a combination of wear parts like blow bars and impact plates.