Helical Pile Helps Hetian Xinjiang Thermal Power Plant Output Project
In this phase, a new 220 kV power transmission line from Hetian Thermal Power Plant to Guanjing Substation will be built, with a voltage level of 220 kV. Two single circuits will be erected in parallel, and only double-circuit terminal outlets will be used on the viewing substation side. At the same time, in order to avoid crossing and crossing, the Puguan 220 kV line (Luopu Substation-Guanjing Substation) needs to be rebuilt, and the length of the reconstruction section is 0.426 kilometers. A total of 31 towers are used on the whole line, including 14 single-circuit tension towers, 16 single-circuit straight lines, and 1 double-circuit tension tower.
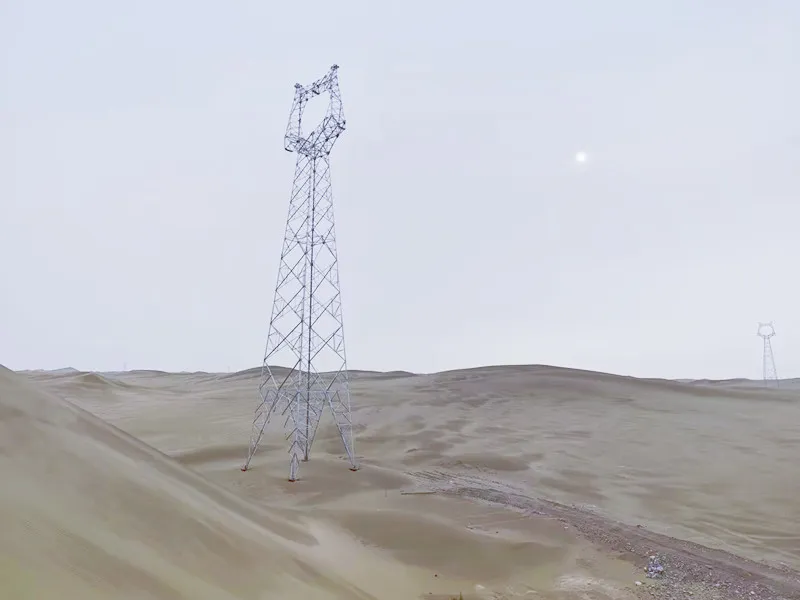
The pile foundation of the electric tower does not use the common concrete pouring pile, but chooses the helical pile foundation with a shorter construction period and more convenient installation. The helical pile is also called the screw anchor. The screw anchor foundation technology can realize the cutting and screwing of the foundation soil through the spiral structure of the anchor plate and the installation torque acting on the top, so as to make full use of the resistance of the deep soil and improve the strength of the foundation. carrying capacity.
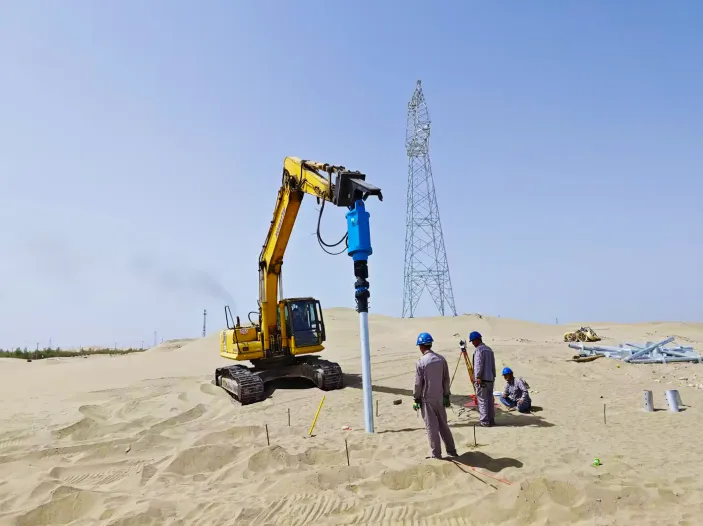
At the construction site, the helical pile informatization installation system provided by Yichen Company is in operation. The whole construction process is simpler than the traditional pile foundation construction method. Usually divided into the following steps:
No.1 Ground preparation: Before proceeding with the installation of helical piles, the ground needs to be prepared. This includes clearing the site to make sure there are no obstructions or debris preventing the installation process.
No.2 Pile position calibration: according to the design requirements, the position of each helical pile is calibrated on the ground. These locations are usually determined by engineers based on design drawings and calibrated using measuring tools.
NO.3 Pre-drilling: At each pile site, pre-drilling is carried out using equipment such as a drill rig or an excavator. The depth and diameter of the pre-drilled holes should meet the design requirements to ensure the installation quality of the helical pile.
NO.4 Helical pile installation: Connect the top end of the helical pile with the excavator and insert the helical pile into the pre-drilled hole. The construction personnel rotate the helical pile by manipulating the excavator and gradually push it into the ground until the required installation depth is reached. During the installation process, the installation torque and thrust need to be monitored to ensure the correct installation of the helical pile. Yichen Company has installed a torque monitor and a verticality monitor on the construction system, and the data is transmitted to the cab of the excavator in real time, so that the construction personnel can perceive the construction situation in real time and make timely adjustments.
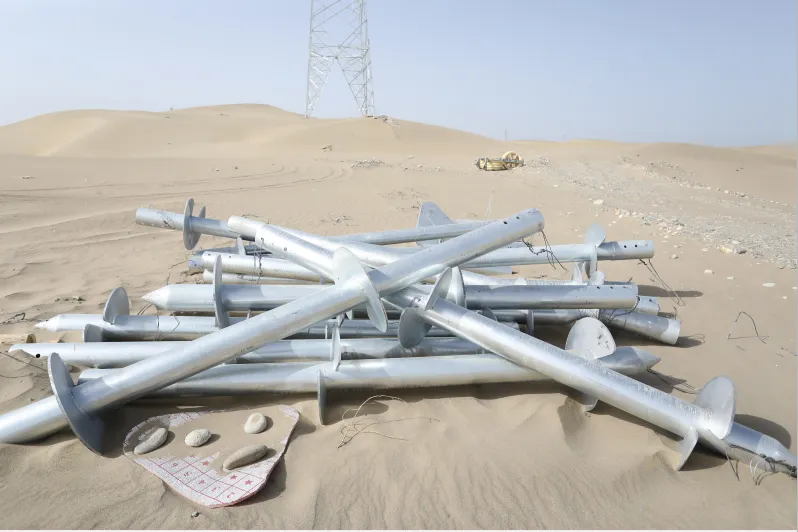
NO.5 Pile head treatment: After the installation is completed, the top of the helical pile should be treated according to the design requirements. Includes caps and other structures welded to the base of the tower.
NO.6 Quality inspection: Carry out quality inspection to ensure that the installation of helical piles meets the design requirements and relevant specifications. This may include checking installation depth, installation location, levelness, etc.
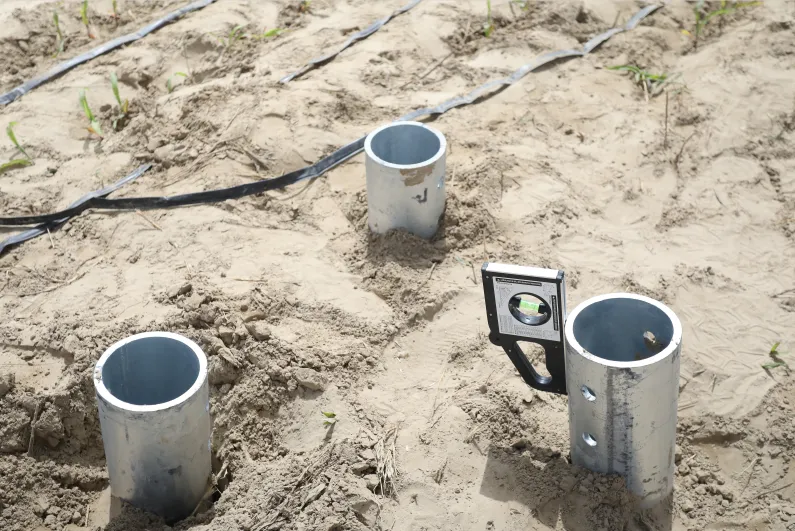
Helical pile foundation technology is a highly efficient, environmentally friendly and economical foundation construction technology. It can be applied to various soil environments, including silt, cohesive soil from fluid plastic to hard plastic state, loose to medium sandy soil and gravel soil, as well as special soil layers such as loess and soft soil. It has the characteristics of large pile bearing capacity and corrosion resistance, and can meet the requirements of uplifting, pressing down, and horizontal bearing capacity of the foundation of high-voltage electric towers. At the same time, this process can reduce the impact on the surrounding environment, will not generate noise and vibration, and will not affect the soil structure and water source. In addition, because this process can realize fully mechanized construction, it can also reduce the demand for human resources, improve construction efficiency, and reduce construction risks, thereby ensuring the quality and safety of the project.