Essential Guide to Mini Excavator Inspections- Hydraulic Pulverizer
Keywords: concrete pulverizer for excavator, mini excavator auger
According to the Occupational Safety and Health Administration (OSHA) and Bureau of Labor Statistics, there are over 18,000 heavy loading injuries in America. While nobody wants equipment accidents to happen on their site but unfortunately they do happen. A great way to lower the risk and injury is to schedule routine safety checks of your equipment, including mini excavators.
This is your comprehensive guide to mini excavator inspections. Performing routine inspections on your equipment ensures the safety of your crew and the longevity of your equipment.
Recognizing the Importance of Regular Mini Excavator Inspections
Performing routine maintenance benefits your job sites in more ways than one. Inspections help prevent accidents, ensure optimal equipment performance, and extend equipment lifespan, keeping your job site both functional and safe. Completing different types of inspections including initial inspections, frequent inspections, and annual inspections encourages longevity and efficiency of equipment.
4 ton, Mini Exavator Rentals
1.5 ton – 9 ton
5 ton, Mini Excavator Rentals
1.5 ton – 9 ton
6 ton, Mini Excavator Rentals
1.5 ton – 9 ton
Having a routine for scheduled and preventative maintenance can lower repair bills by 25%. By detecting minor issues that may typically slip under the radar, regular inspections can prevent expensive repairs that delay production.
If you don’t feel confident in keeping these machines up to OSHA standards yourself, then go through a rental marketplace like DOZR. Equipment rental companies on DOZR all ensure that the equipment you are renting is up to all OSHA codes. Allowing you to focus on the job at hand.
Implementing Daily Mini Excavator Inspections
It is strongly recommended by both manufacturers and OSHA to complete thorough inspections of your mini excavators on a per-shift basis. Conducting inspections before using a heavy loading machine helps prevent expensive repairs.
One way to guarantee that every component of the machinery is inspected is to have a checklist. Your checklist should include evaluating the different operating systems, safety devices, structural components, and more. Most manufacturers have specific checklists for you to follow and it’s best to refer to them when you can.
Visual Inspections and Check for Dents, Bends, or Cracks
While there are many problems that can be hidden within the cab of a mini excavator, it’s possible to find them during a visual check. Damage to the external body of a mini excavator on the body, undercarriage, and track, can be indicative of internal issues. These issues include track tension issues, impact damage, or misalignment.
A damaged undercarriage can result in many different issues. These issues include the misalignment of tracks or other components, leading to reduced stability, uneven wear, and future functional issues. This misalignment can occur due to collisions, rough terrain, or improper operation.
This type of damage can cause multiple issues including improper tensioning of tracks. This reduces the machine’s efficiency and can worsen the condition of the machine
The implications of these damages include reduces job site efficiency, high costs, and further damage to your machine. The required actions to take with these issues is to assess the damage, consult the manual, and proceed as directed. These resources provide valuable and insightful information on the machinery, and the direction may change depending on the issue at hand.
Engine, Fluid Levels, and Hour Meter
Checking your mini excavator’s oil, coolant, and hydraulic fluid levels, keeps your equipment performing properly. With each fluid serving a different purpose, they are all essential to the functionality of the machine. Lubricating moving parts, cooling the engine, or working within the hydraulic system, they help to maintain efficiency, power output, and more.
Engine leaks should be carefully observed as different fluids may leak from various locations on the machine, impacting it differently. For example, if there are low hydraulic fluid levels it can result in reduced lifting capacity and compromising the operator’s safety.
Hydraulic System Leaks
Inspecting the hydraulic pump compartment, cylinders, lines, and hoses for leaks is an essential part of any mini excavator inspection. Unusual fluid loss can indicate an underlying issue in the mini excavator, such as leaks, damaged seals, or malfunctioning components. Taking proactive measures, including daily inspections, can help avoid costly repairs or delays.
Some of the most common locations for leaks include swivel joints, swing bearings, and slew rings. Leaking at any of these points can be caused by factors like gradual wear, insufficient maintenance, or exposure to harsh conditions.
However, each can cause a different issue. A leaking swivel join results in hydraulic fluid loss, and leaking swing bearings and slew rings result in lubrication loss. With timely action, you can prevent damage to the core components of your mini excavator from any of these leaks occurring.
Inspect for Scalloping and Lifespan on Attachments
Scalloping, or “tooth shatter,” is a wear pattern found on the cutting edges of the bucket’s teeth. It is often characterized by uneven wear. It can be easily identified when looking at the teeth of the bucket during a visual inspection.
Rent a Mini Excavator
Depending on the severity of the scalloping and the condition of the teeth, some actions can be taken to fix the attachment. Including sharpening the cutting edges, replacing individual teeth, or replacing the entire bucket if necessary. It’s important to follow the maker’s guidelines or consult with a professional technician to determine the best course of action.
Conducting Regular Maintenance Inspections
Having a planned schedule for your machines’ maintenance reduces the chance of surprise mechanic visits, that will delay your production. Following an inspection checklist and manufacturer’s manual, and having your mini excavator’s spec guide on hand, will help increase productivity and equipment longevity.
Some of the areas that you’ll need to make sure you check out during these inspections include the engine, undercarriage, tracks, and key connection points. These are all important areas of your mini excavator that must be functioning properly for efficiency and safety.
Engine and Fuel Systems
If you fail to complete regular services for your mini excavator’s engine you’re increasing its repair costs and decreasing its lifespan. Undetected issues will worsen over time and increase in cost, while potentially delaying your schedule. Regular inspections of your engine and fuel system, whether electric or non-electric, are important. These inspections catch issues before they delay production or become expensive.
Undercarriage and Tracks
Incomplete routine checks on the track and undercarriage can result in wear and tear getting out of hand. Causing loosening or improperly tensioned tracks, reduced efficiency causing unnecessary wear & potentially derailing or slipping.
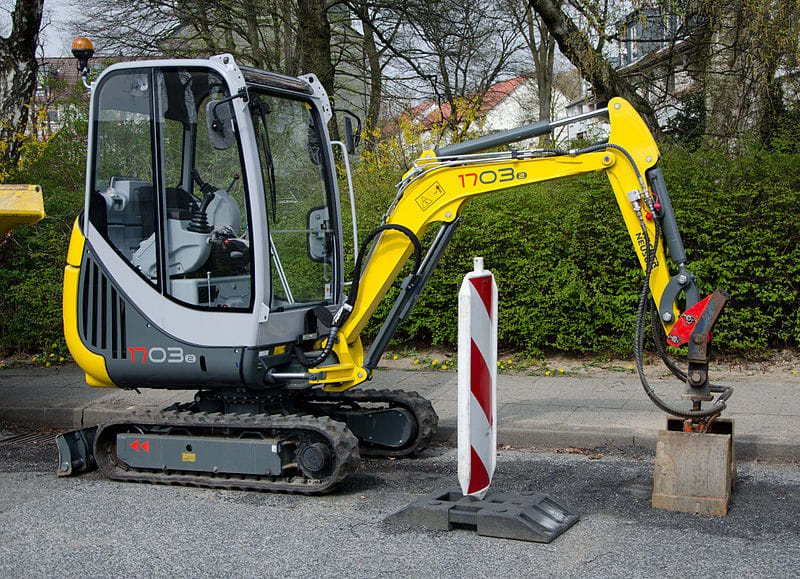
Sprockets positioning on a mini excavator determines the tension of the track. If a sprocket loosens, then there will be an increase in risk on the job site. In addition, there will be premature wear and tear to the track, decreasing its lifespan. This is why checking the undercarriage and tracks is so significant in its routine maintenance.
Repair Welds and Connection Points
Ensuring that your welds and connection points are functioning is crucial for your mini excavator. Critical stress points are extra vulnerable to fatigue and other types of damage. This means that if left unchecked, your machine’s structural integrity is at risk. Routine inspections can help in uncovering serious structural issues before they become delayed and expensive.
Connection points can be another important structural component to check on. Ensuring that they are properly fastened, lubricated, and more is important in protecting you and those on your site. Additionally, making use that you have the best attachment for your mini excavator is key to productivity on your site.
Importance of Annual Professional Inspections
Having a qualified professional inspect and repair your mini excavator is important. Knowing the equipment back and forth helps them identify issues or potential issues, that the untrained eye may overlook.
Annual inspections conducted by qualified professionals help ensure compliance with industry regulations, safety standards, and legal requirements. By having a qualified individual, either internal or external, service your equipment, you can demonstrate compliance with legal and regulatory standards.
Record Keeping and Documentation
Maintaining accurate documentation showcases its condition over time and keeps track of different issues that arise but also helps ensure consistency. These documents include inspections, repairs, and maintenance. Consistency in inspections and the care of your machinery through documentation can help ensure your compliance with OSHA regulations.
When selling or trading in your machine, it’s beneficial to keep track of your machine’s repairs, maintenance, and inspections. A well-maintained machine is able to be sold between 40-60% of its retail price.
Ensuring Safe and Efficient Mini Excavator Operations
This guide provides a comprehensive overview of mini excavator inspections, emphasizing the importance of conducting regular checks. Ensuring the safety of your crew by performing routine inspections on your equipment, enhances the durability, and lifespan of your machinery.
Rent a Mini Excavator
Accidents on the job site and increased risk due to the absence of scheduled routine checks for mini excavators are often overlooked. When renting through DOZR Marketplace, you will know that the machine will show up in great condition. However, if you’re renting for an extended period of time, it’s important to continue to do daily inspections documentations. This will help you return the machine in great condition.